I went into a small toy and stationery store to make a photocopy. There was a huge sign over the door “DRUCKEREI PAFFENHOLZ” and since “Druckerei” means printer, I thought I’d find a copy shop. (LOL!)
“The office is in the back,” the salesperson told me, so we went through a door and walked past a row of large printing machines.
This wasn’t a mere copy shop.
But when I asked about a small print job, Mr. Paffenholz offered us a tour of the whole place.
Yes, please! 🙂
Later, I found out this family business has been active for 50 years! That’s a lot of paper and ink!
The first step in producing a printed book is a shoot-out: the pages are “ausgeschossen” which means literally “shooting the pages out”. It’s not the wild west, it means the pages are laid out for printing on larger sheets. Some pages are right side up and other pages are printed “standing on their heads” so that the pages will all be in the right order and orientation in the finished book.
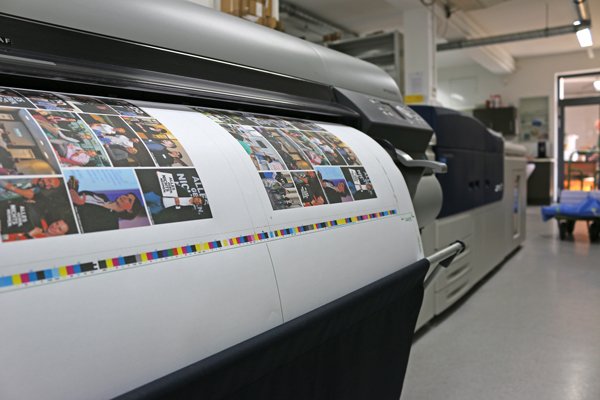
For this, the printer uses a digital printing machine that uses the same technology as “print-on-demand” and handles very short print runs, like groups of 50 or 100. I think they also use this machine to check the incoming InDesign files and print-ready PDF files that come directly from customers or from their in-house graphic designers.
Then we toured the off-set printing process.
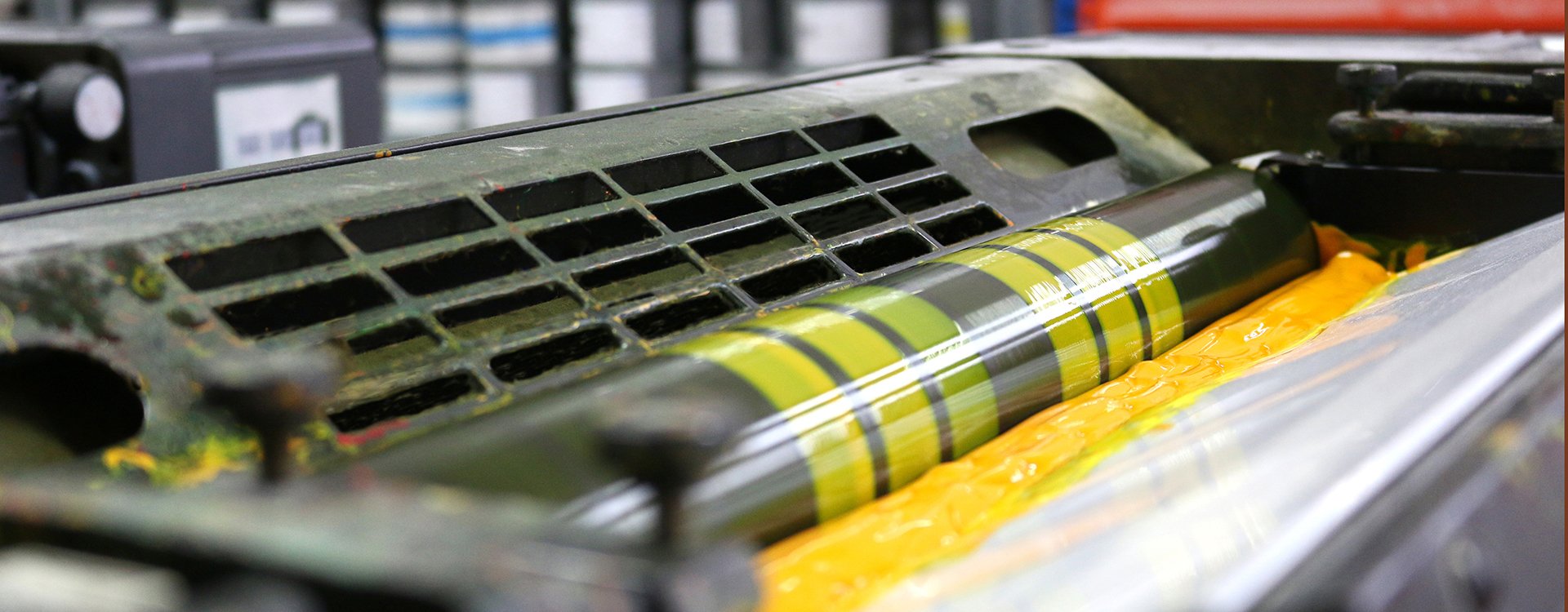
The next step was a machine that creates the metal plates for the four-color printing process (CMYK or Cyan, Magenta, Yellow or Key–short for Black). One aluminum plate is etched with the design for each color. Later, the metal plates are recycled.
Of course, I was trying to imagine how I could make a coffee table or something out of them, if I ever had a book printed on an off-set press! Authors are a little strange.
The next machine was shaking a stack of pages together to make them even. It’s like what you do when you bang a ream of paper on the counter to make it “square.” Every so often, the machine operator added a heavier piece of construction paper to the pile. I’m not sure if that was to separate each edition of the book being printed or if it was to weigh the other pages down.
Another machine cuts the pages to size once they’ve been shaken together.
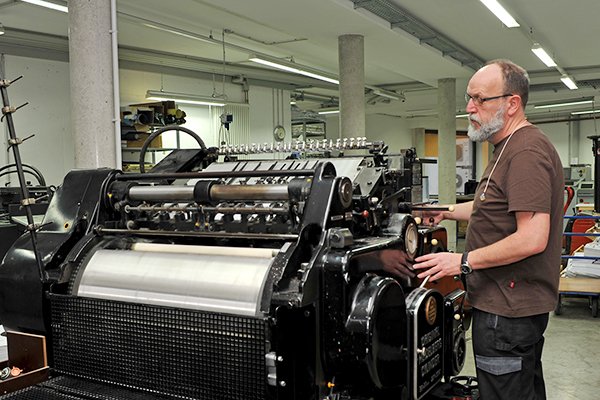
Older machines in the back of the hall could still handle embossing, punching, glue-ing. I’m not sure if they can do Braille, maybe not.
Wouldn’t you love to have a Braille edition of your book? Oh, look what Google found for me: http://www.braillebookstore.com/Braille-Printing Now I have a new ambition. 🙂
Then we went back up to the room-sized machine that prints the CMYK colors using the metal plates created by the other machine. When the metal plates are wet, the etched design is the only thing that takes up ink. Each metal plate does one color.
The paper travels through four connected printing machines like a ticket collector going through the cars of a train. (See photo of company staff above.)
Dodging a small fork-lift, we looked at the control station where the printer adjusts the color settings until they get the effect they want.
“What do you think? A little more Cyan?”
The folding and stapling machines to make the finished brochures and booklets were last on the tour.
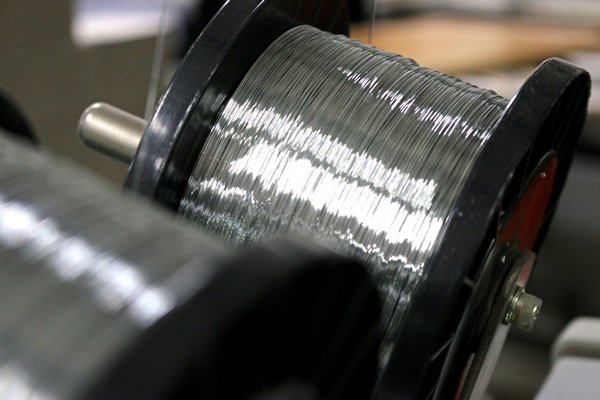
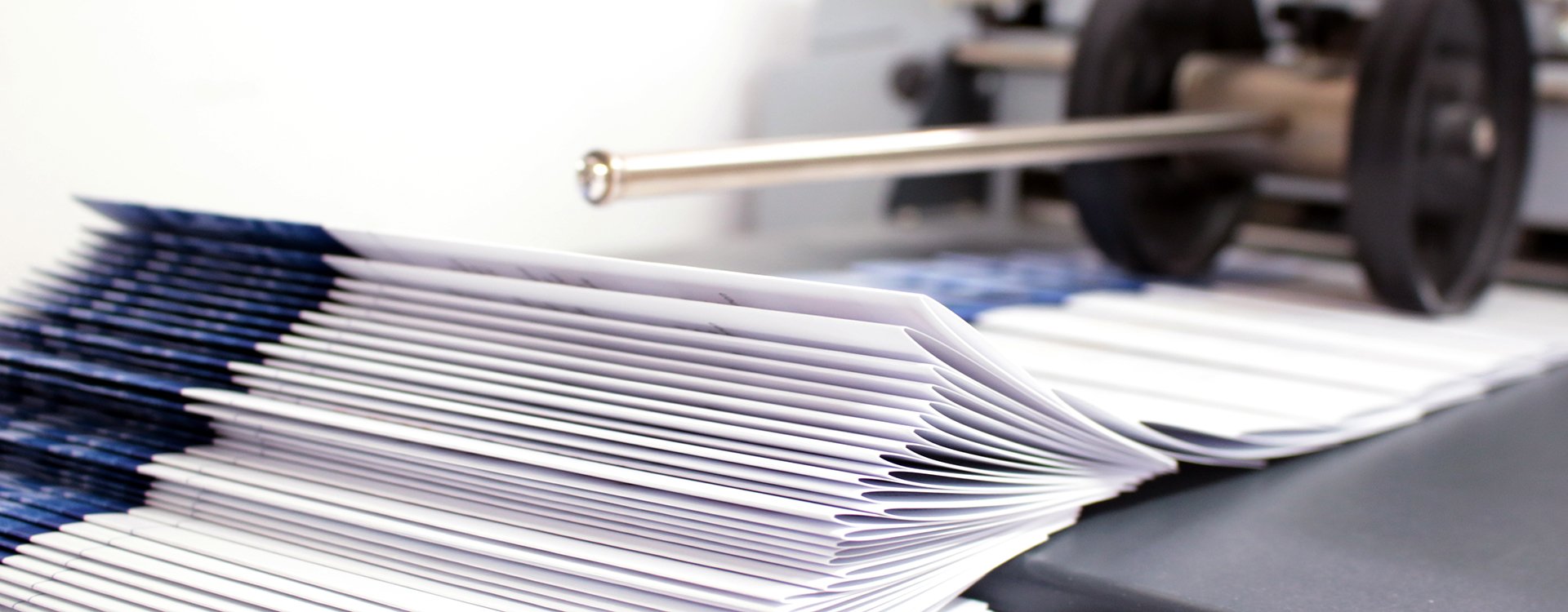
NOTE: I didn’t have a camera so I couldn’t take photos even though Mr. Paffenholz gave me permission. The photos here are all from the Druckerei Paffenholz website.
When I got home, I found this book, a perfect combination for a printing family that runs a toy and stationery store!
Hope you enjoyed the tour!